Waste disposal is one of the major problems being faced by all nations across the globe. The daily per capita solid waste generated in India ranges from about 100 g in small towns to 500 g in large towns. It takes anywhere between three and seven days for the waste to be disposed from the time of its generation. Major portion of the collected waste is dumped in landfill sites. The recyclable content of waste ranges from about 13% to 20%. In a developing country like India, paper, plastic, glass, rubber, ferrous and non-ferrous metals all the material that can be recycled are salvaged from this waste to produce low-cost products extensively used by the lower-income groups of the society. However, data collected from 44 Indian cities have revealed that about 70% of them do not have adequate capacity for collection and transportation of MSW (municipal solid waste) (Pachauri and Sridharan 1998). The uncollected waste that usually finds its way in sewers is eaten by the cattle, or left to rot in the open, or burnt on roadsides.
In the face of burgeoning urban populations and growing mounds of garbage, initiatives like converting garbage into energy could show the way for cities. A private company has begun converting the city's garbage into fuel pellets and now plans to establish a 10 MW power plant. According to TIFAC (Technology Information Forecasting and Assessment Council), Delhi, Mumbai, and Calcutta would be generating 5000 tonnes of garbage every day, in about a decade, and disposal would be difficult. The existing dumping years would create enormous pollution and health hazards. Municipal authorities would find it expensive to transport garbage and dispose it of scientifically, according to a TIFAC data sheet on 'Fuel pellets from municipal waste'. As part of a pilot project for integrated waste management, the Department of Science and Technology had established a prototype fuel pelletization plant at Deonar, Mumbai, in the early 1990s. The plant was designed to process Indian garbage. The garbage was first dried to bring down the high moisture levels. Sand, grit, and other incombustible matter were then mechanically separated before the garbage was compacted and converted into pellets. Fuel pellets have several distinct advantages over coal and wood, according to the TIFAC data sheet. It is cleaner, free from incombustibles, has lower ash and moisture contents, is of uniform size, cost-effective, and eco-friendly (The Hindu, 2 May 2000).
Table 1 Estimated quantity of waste generated in India
In addition to MSW, large quantity of waste, in both solid and liquid forms, is generated by the industrial sector like breweries, sugar mills, distilleries, food-processing industries, tanneries, and paper and pulp industries. Out of the total pollution contributed by industrial subsectors, 40% to 45% of the total pollutants can be traced to the processing of industrial chemicals and nearly 40% of the total organic pollution to the food products industry alone. Food products and agro-based industries together contribute 65% to 70% of the total industrial waste water in terms of organic load (Pachauri and Sridharan 1998a). Table 1 gives an estimate of waste generated in India by various sectors and industries.Source Bakthavatsalam (1999)
Waste Quantity Municipal solid waste 27.4 million tonnes/year Municipal liquid waste (121 class I and II cities) 12145 million litres/day Distillery (243 nos) 8057 kilo litres/day Pressmud 9 million tonnes/year Food and fruit processing waste 4.5 million tonnes/year Willow dust 30000 tonnes/year Dairy industry waste (COD level 2 kg/m3) 5060 million litres/day Paper and pulp industry waste (300 mills) 1600 m3 waste water/day Tannery (2000 nos) 52500 m3 waste water/day
In addition, the daily per capita sewage generation is about 150 litres. The total sewage generated in India, about 5 billion litres/day in 1947, grew to 30 billion litres/day in 1997. However, the total treatment capacity available is only about 10% of this quantum generated. It is estimated that under the Ganga Action Plan, 46 000 Nm3 (normal cubic metre) of biogas can be produced daily from the sewage treatment plants in 21 Indian cities by treating about 339 million litres/day of municipal waste water. This, with appropriate biogas power plants, will generate total electrical energy of 99 450 kWh/day (Singh 1996).Table 2 Estimated renewable energy potential in India
The urban municipal waste (both solid and liquid) industrial waste coming from dairies, distilleries, pressmud, tanneries, pulp and paper, and food processing industries, etc., agro waste and biomass in different forms if treated properly, has a tremendous potential for energy generation as shown in Table 2.Source Bakthavatsalam (1999)
Energy source Estimated potential Bio energy 17000 MW Draught animal power 30000 MW Energy from MSW 1000 MW Biogas plants 12 million plants
Last year, the INSWAREB (Institute of Solid Waste Research and Ecological Balance) came up with the theory that rice husk, a cheap by-product of paddy milling, has the potential to galvanize the electricity-starved rural India. With a gross calorific value of 3000 kcal/kg, rice husk, capable of high-efficiency combustion, could serve as the fuel for mini power plants of 1 to 2 MW capacity that can be set up in rural areas. The RHA (rice husk ash), obtained as a by-product by burning it, can generate power in the process.
The cost of establishing and maintaining the mini power plant can be easily made good by exporting RHA, which can fetch $50 a tonne. INSWAREB has drawn an action plan for promoting RHA fully exploiting its export potential. It proposes to initiate a couple of mini power plants to popularize the theme. (The Hindu, 9 February 1999).
Similarly, at an inter-ministerial meeting involving the ministries of power, environment and forests, and urban affairs and employment, it was decided to encourage the use of fly ash bricks in all construction activities. The NTPC (National Thermal Power Corporation) had thought of setting up two fly ash brick manufacturing plants at Badarpur and Dadri near Delhi; the theory being that fly ash, apart from being used as a substitute for bricks, could also be utilized for the embankment of roads.The enormous amount of ash generated in Indian thermal power stations poses a serious threat to the environment. In principle, this problem can be tackled by using fly ash in building construction. Increased awareness and use of fly ash bricks, which is stronger (100 kg/cm2 compared to 5075 kg/cm2 of conventional bricks) and smoother on the sides (reducing plastering costs significantly), can provide an eco-friendly solution. Fly ash bricks are better than traditional bricks in the sense also that ash bricks do not use the top fertile soil of the earth, thus protecting the land from agricultural use. Located at the south-east corner of Delhi, the BTPS (Badarpur Thermal Power Station) meets more than 25% of the energy consumption of the capital. It also produces a staggering amount of ash every day (almost 5000 tonnes). The station has, however, been making concrete efforts in ash utilization as a responsible corporate citizen. It has given a major thrust in ash utilization through the manufacture of bricks from fly ash. At present, it has seven units given to private contractors, which manufacture around 16 000 bricks every day. The BTPS had installed a pilot-cum-demonstration plant at its ash dyke way back in 1993. The station adopted the FAL-G technology for the manufacture of ash bricks, which does not require firing or autoclaving. These bricks require natural drying and hence are totally energy-efficient and environment-friendly (The Financial Express, 4 April 1999).
It was also estimated that an energy-from-waste plant, which was to be set up in Scotland, would annually convert 120 000 tonnes of the city's municipal and commercial waste into electricity. It as also to deal with small amounts of non-hazardous clinical and liquid wastes. Besides generating adequate electricity for the plant's in-house needs of around 2.2 MW, it would sell 8.3 MW to the National Grid, electricity distribution network of UK. The facility incorporated two separate systems fuel processing and combustion.To produce the fuel, incoming waste is fed into one of the two hammer mills, where it is shredded into coarse floc material. Each of the mills handles 30 tonnes of waste an hour, almost double the plant's throughput of 15.6 tonnes an hour. The over-capacity allows for unplanned downtime. Magnets remove ferrous materials before the floc is carried by conveyor to a fuel-storage building capable of holding enough for two days operationabout 800 tonnes of refuse-derived fuel (The Hindu, 21 October 1999).
Scientists have developed a technique to treat foul-smelling polluted distillery wastes, using energy from the sun and a chemical catalyst. Tests on a small laboratory-type reactor showed that the method can detoxify 100 litres of diluted distillery waste water in five days. Results of the project at the NARI (Nimbkar Agriculture Research Institute) at Phaltan in Maharashtra were submitted to the MNES (Ministry of Non-conventional Energy Sources). The scientists had applied for a patent on the chemical catalyst. The emphasis after this was to try to improve the technique so that waste treatment is over in just two days. The NARI scientists had taken cues from work on solar detoxification of ground-water and industrial wastes using titanium dioxide catalyst.
By purifying biogas produced from distillery wastes, scientists claimed to have generated huge quantities of com-pressed methane, a gas with immense potential as an alternative source of vehicle fuel. Experimenting with bulk distillery wastes from alcohol manufacturing breweries, researchers from the chemical engineering department of the Jadavpur University produced the gas by a process called biomethanation of the effluents. The process, which also cuts down on the environment pollution, has proved to be an eco-friendly energy production method (The Observer of Business and Politics 25 April 2000).
TERIscientists has been developing new technologies to tackle the problem of waste management
TERI has developed a high-rate digester for fibrous and semi-solid municipal waste with the promise of revolutionizing the waste disposal industry. Described as TEAM (TERI Enhanced Acidification and Methanation) process, for which the patent has also been filed, the digester is said to be quick, economically viable, and suitable for food and agro-based industries and markets. In the face of evident environmental drawbacks of waste disposal methods like land-filling and incineration, the process of biomethanation of waste by anaerobic digestion has economical and social benefits apart from being environment-friendly (The Hindu, 18 March 2000).
TERI began work on the development of a high-rate digester for fibrous and semi-solid MSW in 1996. TEAM process is the culmination of these efforts. The salient features of TEAM are listed below.
Lowered retention time (7 days) and plant area for the whole process to make it economically viable as compared to conventional single phase reactors (3040 days) or aerobic composting (3 to 6 months)
Complete elimination of engineering problems like scum formation, floating of feed leading to incomplete digestion, feed flow problem, etc.
Technology suitable for adoption by small entrepreneurs
Low water consumption because of reuse of the UASB reactor overflow to acidification reactor
Production of good quality biogas, which can be used for power generation or thermal application like cooking or production of process steam as per the needs,
The decrease in total volume of the feed stock after decomposition is more than 50%
The residue after drying is good organic manure.
Currently, a bench-scale plant for processing 50 kg of vegetable waste per day is operational at the Gual Pahari campus of TERI, at Gurgaon, and efforts are under way for upscaling.
The wastes generated by various sectors need to be assessed and evaluated for their energy potential or reuse in any other form. Biomethanation has emerged as the best option for the treatment of high organic content liquids for energy generation. The use of this technology to Indian MSW is still in its developmental stage. Once a commercially proven technology is established, it will go a long way in dealing with energy problems in the country.
SEARCH THIS BLOG
Wednesday, November 30, 2005
Re: energy recovery from dairy waste
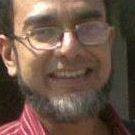
Tuesday, November 22, 2005
Why I quit Indian Idol II
I called a friend, a guy I refer to as my spiritual guide. All he said was that if there was no passion in it, and if I was in a "don't know" zone, maybe it wasn't for me. He was right. I had never had much to do with singing. I had tried learning from two gurus in the past, both of whom I had run away from. So, why spend time with people who clearly knew little about music let alone 'launching' talent and compete for something I didn't want in the first place? Just to make my neighbours happy?
Turning to my colleague, I told her I had to get out. I hugged her, wished her luck and left.
Looking back, those eight hours changed my life. I stood up for myself. I felt good about the fact that no one managed to take my laughter away from me. I could giggle as much as I wanted to.
A few people still refer to me as 'Idol'. I'm hoping they stop. Soon. I can see no pride in being someone who smiles when he or she is told to. I don't need a title for being someone's puppet. I like my own title, Archana Pania! And, you know what, I don't need a million votes to burst into song whenever I feel like either...
Archana Pania is the resident jockey at Rediff Radio and got through two rounds of Indian Idol II.
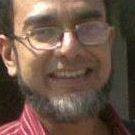
Wednesday, November 09, 2005
http://www.haithindustrial.co.uk/index.php?sec=news&news_id=9
SUBMERGED AERATED FILTERS WITHIN PACKAGE TREATMENT PLANTS.
23 September 2003
Package Treatment Plants are largely known as a solution for single households, or a few houses, to replace septic tanks in rural communities where alternatives to mains drainage becomes impracticable or uneconomic. However, they are increasingly being used as a solution for larger flows, including municipal wastewaters and industrial effluents.
The Urban Waste Water Treatment Directive demands that water companies must improve small and medium, waste and water treatment plants that supply less than 15,000 population, this also includes increased capacity for ammonia removal.
In contrast to conventional sewage works designed on a bespoke basis using concrete, package sewage treatment plants are prefabricated systems incorporating single or multiple treatment stages. With the latter, this is usually primary sedimentation, secondary biological treatment and final settlement incorporated into a single, compartmentalised tank. As a complete package, these systems offer a low cost alternative in terms of design, capital cost and installation for small to medium-sized sites.
Generally, the design philosophy for package treatment plants is dependant on the flow to be treated. Plants above 100 PE are designed on a modular basis whereby each treatment process is contained within its own tank. This allows a greater flexibility in the design to suit the raw sewage characteristics and the final effluent requirements of the project. Newer designs that incorporate submerged aerated media mean that this size range is likely to be increased.
While most systems use the sedimentation process for primary treatment as well as final clarification, they can be differentiated in their choice of biological unit operations for secondary treatment, which are usually one of three options:
a)Enclosed Trickling Filters
b)Rotating Biological Contactors
c)Submerged Aerated Filters (SAF)
In three recent projects Haith Industrial have provided a package solution utilising SAF units. There proven experience in the supply of SAF units has found that they provide high performance due to their robustness and tolerance to flow and load variances.
For this reason Haith Industrial select an attached growth system carried out in an SAF Unit. Attached growth, which is where the micro-organisms are attached to random packed media as well as the effluent, percolates through the media undergoing purification during its passage. The micro-organisms grow in flocs; these flocs are responsible for the transformation of the organic material into new bacteria, carbon dioxide and water.
Haith have found that such systems are simple to operate and have low operating costs and have the ability to withstand shock and toxic loads owing to the relatively short contact time of the effluent with the slime layer. However, what is seen as the SAF units great attraction is its low maintenance and management requirements.
Haith say that being high rate, the main advantages of the SAF Unit are reduced power and maintenance costs, stability against hydraulic shock loads, and a capability of achieving a high degree of carbonaceous and nitrogenous BOD removal.
Additionally, ponding of the bed and clogging of filter nozzles is eliminated and odours and fly nuisance are also eradicated.
Project One SAF unit alongside existing plant.
This project required the supply of two SAF modules operating in parallel with existing mineral filter beds in the location of a demolished unit.
Each of the units was manufactured from 5mm stainless steel plate and incorporated sealed roof with closed cell gasket, air blower unit including pressure relief valve, inlet silencer and air flow meter. Additionally a diffused air distribution system mounted on quick access cassettes, random media, media retaining decks and media supporting decks was included.
Both units were sized to treat 32.5% of the flow to the works; in order to establish the specification and size, Haith modelled the process by applying each of the determinants of the consent to highlight the drivers for the system. The calculations revealed that the drivers are a combination of the retention time to achieve nitrification and the BOD/media loading rate to ensure compliance with the Generic SAF Plant Specification. In this project each SAF unit was fed by gravity from a distribution chamber, within this vessel, adjustable weir plates provide an even distribution of settled sewage to each SAF for treatment. Following treatment through the plant the treated effluent will gravity flow to two conical humus tanks.
Built in stainless steel fabricated modules, each factory assembled and tested to allow quick assembly, Haith recommended above ground installation which would require only minimal ground works; access to the aeration equipment would be a simple operation of removing a set of bolts and sliding out the aeration cassette.
Each SAF module has the hydraulic capacity of approximately 4 litres per second, and was designed to the following plant data:
PE 650
Dry weather flow 1.2 litres/sec
Full flow to treatment 2.9 litres/sec
Settled BOD load 26.2 kg/day
Ammonia load 3.6 kg/day
Effluent discharge standard:
20mg/1 BOD (95% ile)
7 mg/1 AmmN (95% ile)
51mg/1 SS (95% ile)
The design of the Haith Aerated Treatment Unit (SAF) is a fixed film reactor for the oxidisation of the BOD and ammonia. As such the micro-organisms are attached to high voidage plastic media, which is random packed to prevent short cutting. Each unit has three compartments with the media selected for each compartment to provide the correct surface area/BOD/oxygen ratio.
In this project, the first compartment was fitted with lower surface area media than the following two; this provided a robust process operating at maximum efficiency with a minimum requirement for backwashing.
The unit was modular built with all ancillary equipment, membrane air diffusers, media and internal baffle plates fitted in the factory. This enabled the filter to be transported to site as an operational unit ready to run following connection of supply and discharge pipe work and the air supply equipment.
The filter was the Haith standard multiple cell upward flow design, each cell being of equal size. Stainless steel ambideck panels mounted in a common frame supported the bacteria supporting media in each cell. Additionally a holding down deck was secured to the top of the filter to retain the swelling media during the establishing period.
Aerobic conditions were provided in each cell by an aeration system comprising of E.D.P.M. membrane diffusers mounted on a manifold, which in turn was connected to a centrifugal type air blower set. Each manifold comprised of a number of feeder and cross pipes extending through an access door which in turn was bolted to the filter wall. The complete assembly of manifold and aeration diffusers can be drawn clear of the filter by removing the door bolts, allowing inspection and maintenance without the need to remove the media.
A sectional cover was provided, designed to span the width of the filter without the need for immediate supports. The centre cover was equipped with a water curtain to prevent the release of foam; this was fed by a submersible pump housed in the discharge launder.
Project Two Below ground modular package plant.
In a second project Haith supplied a stainless steel fabricated package plant, comprising Primary Settlement Tank, SAF module and Final Settlement Tank, which were manufactured and delivered to site as separate modules, these were built as a single package plant on site and connected by pipework below ground.
This package plant was designed to the following plant data:
PE 250
Dry weather flow 64m3/d
Full flow to treatment 142.9m3/d
The primary settlement tank was designed in accordance with BS 6297 which ensured an upward flow velocity of no more than 0.9m3 per m2 per hour at full flow to treatment.
The tank was manufactured as an integral part of the module with a hopper bottom of steep valley angles which encouraged the sludge to compact and concentrate, additionally assisting in its movement toward the sludge gulper suction pipe.
The sewage inlet and outlet arrangements in addition to baffle plates contained the scum layer, which was removed along with the co-settled sludge.
Provision was also made for the introduction of humus sludge, which is returned from the final tank at regular intervals to be co-settled with the crude sludge.
The Haith SAF Unit was designed as project one.
The final settlement tank for this project was also designed in accordance with BS 6297 which dictates the surface loading and the retention period of the tank.
This tank also had a hopper bottom with valley angles of 60ยบ which prevents the sludge becoming trapped where it may go septic causing sludge rising problems.
This allows the sludge to be transferred back to be co-settled with the crude sewage by a lift pump which operates either manually or by timer, frequent humus sludge return is necessary to avoid flotation of the solids caused by denitrification of highly oxidised effluents.
Project Three Package plant as one module.
In a third project Haith supplied a package plant with the three main elements as one module. The module was split into three main sections, Primary Settlement Tank, SAF unit and Humus Tank.
This module was supplied factory assembled and tested which provided quick site installation without the need for extensive civil works.
This system was designed for the following plant load data:
PE 120
Full flow to treatment 63m3/day
Dry weather flow 28m3/day
Effluent discharge standard
BOD (SAF) 40 MG/l
Suspended solids 60 mg/l
The design of the Primary Settlement Tank was designed in accordance with BS 6297 as project two.
Design of the Haith SAF unit was as previous; however on this project the unit was housed in the centre of the package plant being gravity fed from the Primary Settlement Tank via a series of internal baffles to prevent the carryover of solids into the SAF.
Design of the Final Settlement Tank was again to BS 6297 as previous projects.
Operation of the plant in all three projects is automatic with the minimum of maintenance following commissioning, Haith have found that SAFs that have been in operation in similar applications have proven to work with little to no operator maintenance and intervention.
As the blower runs constantly the standard Haith design houses this in an enclosure which reduces the noise output to 65-67 dBa at one metre.
Haith point out that the only one essential task to be performed by the operator is de-sludging of the primary tank, this will include the removal of the floating scum which if allowed to accumulate could overflow the scum board and carry into the SAF causing blockages resulting in the deterioration of final effluent quality.
Haith, have in all three different projects provided a package solution derived from their proven experience which considered construction optimisation, looked at operating experiences and evaluated cost reductions in relation to traditional solutions. They have provided a more suitable and competitive solution for small site applications than conventional sewage works designed in concrete.
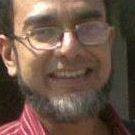