Calculations!:Aeration Tank Volume, HRT, MLSS Values. | |||
I am working in a STP & ETP plant. I need to know how to calculate:
1. Volume of Aeration tank 2. HRT 3. F/M Ratio 4. MLSS value. The relevant details of the ETP are as below: Influent flow = 10 m3 / day In. flow BOD = 1200 mg / L In.flow COD = 2200 mg / L TSS = 850 mg / L Jeyaroopa jeyaroopa79@gmail.com
|
COPY RIGHTS : TO AVOID COPYRIGHT VIOLATIONS, ALL POSTS ARE SHOWN ALONG WITH SOURCES FROM WHERE ITS TAKEN. PLEASE CONTACT ME IN MY EMAIL SALEEMASRAF@GMAIL.COM , IF YOU ARE THE AUTHOR AND YOUR NAME IS NOT DISPLAYED IN THE ARTICLE.THE UNINTENTIONAL LAPSE ON MY PART WILL BE IMMEDIATELY CORRECTED.
I HAVE SHARED ALL MY PRACTICAL WATER TREATMENT EXPERIENCES WITH SOLVED EXAMPLE HERE SO THAT ANYBODY CAN USE IT.
SEARCH THIS BLOG BELOW FOR ENVO ,COMPACT STP,ETP,STP,FMR,MBBR,SAFF,IRON,ARSENIC,FLUORIDE,FILTER,RO,UASB,BIO GAS,AERATION TANK,SETTLING TANK,DOSING,AMC.
SEARCH THIS BLOG
Showing posts with label etp. Show all posts
Showing posts with label etp. Show all posts
Wednesday, January 07, 2009
Calculations!:Aeration Tank Volume, HRT, MLSS Values.
Labels:
Aeration,
aeration tank,
etp,
STP
New Delhi, India
New Delhi, Delhi 110001, India
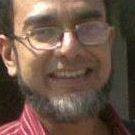
Friday, September 19, 2008
MEAT PROCESSING WASTE WATER TREATMENT LATEST TECH MBBR
Source: http://www.esemag.com/0300/waterlink.html
WASTE WATER TREATMENT: MBBR - MOVING BED BIOFILM REACTOR TECHNOLOGY

MBBR system replaced the chemical pre-treatment system. MBBRs were installed between the equalization tank (EQ) and the activated sludge system. Total reactor volume of the MBBRs is designed for different hydraulic retention time for different types of waste water at average flows and than checked against peak flows. Essentially nutrient levels and DO levels are the only control points for the system.
Effluent from the MBBR is sent to a dissolved air flotation unit, which removes 70-90% of the solids generated, prior to being discharged to the activated sludge system.
The MBBR reactors reduced the incoming organic load from an average soluble BOD by 50-70% . This reduction allowed the activated sludge process to treat the ammonia-nitrogen within the wastewater in a more efficient and effective manner, allowing a higher volume of treated water to be discharged to drain. |

The initial MBBR biofilm unit process shaves the loadings peaks and any toxic inhibition effects while removing 50 to 70 percent of the incoming BOD. This pretreatment achieves 2 to 3 times increased capacity compared to a traditional activated sludge process while also being more compact. Furthermore, the MBBR process improves activated sludge characteristics making the activated sludge stage more inherently stable with a waste sludge that is easier to dewater.
The elements provide a large protected surface area for the biofilm and optimal conditions for the bacteria culture to grow and thrive. The biofilm that is created around each carrier element protects the bacterial cultures from operating excursions to yield a very robust system for those industrial facilities loaded with process fluctuations. The biofilm also provides a more stable "home" for the bacteria to grow, so there is less space required compared to other biological systems and far less controls. An MBBR can be designed for a new facility to remove BOD/COD from wastewater streams or for nitrogen removal. Existing activated sludge plants can be upgraded to achieve nitrogen and phosphorus removal or higher BOD/COD capacity . SALIENT FEATURES OF THE SYSTEM: |
Robust
Trouble-Free
- Easy to Operate
- No Media Clogging
- No Sludge Return
Compact
- Small Footprint
- Low Capital Cost
DETAILED DESIGN & ENGINEERING
- Media Retention
- Aeration Grid
to ~3 ppm.
The bacterial cultures digest the soluble organics, gradually mature, and slough from the media. The cultures form a natural floc
which can be easily separated from the water with the DAF unit. In this case and others, no chemical coagulant or polymer were
necessary to achieve < 10 ppm TSS and over 90% BOD removal.
Saleem Asraf Syed Imdaadullah
Mobile : 9899300371
311/22,Zakir Nagar,New Delhi-110025
email: saleemasraf@gmail.com
BLOG: http://saleemindia.blogspot.com
Mobile : 9899300371
311/22,Zakir Nagar,New Delhi-110025
email: saleemasraf@gmail.com
BLOG: http://saleemindia.blogspot.com
Labels:
etp,
MBBR,
Meat Process,
STP
New Delhi, India
New Delhi, Delhi 110001, India
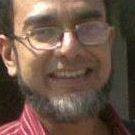
Sunday, September 14, 2008
determinatin of optimum alum dose
INTRODUCTION The main difficulty is to determine the optimum coagulant dosage related
to the influent of raw water. Excessive coagulant overdosing leads to increased treatment costs and public health concerns, while underdosing leads to a failure to meet the water quality targets and less efficient
operation of the water treatment plant.
Manual methods mainly include jar testing
Jar testing involves taking a raw water sample and applying different quantities of coagulant to each sample. After a short period of time each sample is assessed for water quality and the dosage that produces the optimal result is used as a set point.
Operators change the dose and make a new jar test if the quality of treated water changes.
OBJECTIVES
To conduct jar test on a natural surface water in order to estimate an optimum dosage of aluminum sulfate or ferric sulfate for the removal of suspended matter , To observe the rate of floc formation and sedimentation.
The dose of coagulant which gives the best floc is the optimum dose of coagulants.
PROCEDURE
A. DETERMINE OF OPTIMUM COAGULANT DOSAGE- Collect 20 to 50 liters of a natural surface water. Analyze the water for pH, turbidity, color after filtration, and alkalinity.
- Alternatively, make up a synthetic water sample for testing. Record both the water temperature and ambient air temperature.
- Calculate the amount of alkalinity required to react with the maximum dosage of aluminum or ferric sulfate. If necessary, augment the natural alkalinity by the addition of 0.1 N Na2CO3 so that the alkalinity will be at least 0.5 meq/l (25 mg/l as CaCO3).
- Measure exact 1 liter of water into each jar test reactor. Prepare portions of the aluminum or ferric sulfate solution which will yield 10 to 50 mg/l as Al2O3 or Fe2O3 when added to the sample aliquots.
- Mix at 50 rpm to ensure water is completely mixed.
- Measure chemical volumes to achieve desired dose in each reactor.
- Increase mixing speed to 250 rpm. Add the chemicals to each reactor near the vortex. All reactor should be dosed at the same time.
- Rapid mix for 1 min.
- Reduce mixing to 60 rpm for 9 min.; Observe the reactors at 3 min. intervals to detect the formation of flocs. Reduce mixing to 25 rpm for 4 min.; Reduce mixing to 10 rpm for 2 min.
- Turn off mixers and allow particles to settle for 20 min.
Measure the turbidity or color, alkalinity, and pH of the liquid in each jar by sampling at the top, taking care not to disturb the sediment in sampling. Measure the depth of sludge in the beaker.
Measure final pH, turbidity or color of the supernatant of each sample. Measure the depth of sludge in the beaker.
Plot turbidity or color versus pH.
EFFECT OF MIXING (AGGREGATION KINETICS)
Prepare identical (optimum) coagulant dosages for all six beakers.Use the same rapid mix as before but vary the time of slow mix at 30 rpm. Use 5, 10, 15, 20, 30, and 45 minutes for the six jars respectively. Terminate mixing by carefully lifting the paddle from the beaker at appropriate time.
Allow 30 minutes for settling.
Measure the color or turbidity and pH of the supernatant in each beaker.
APPARATUS
Jar test apparatus and beakersMagnetic stirrer plus magnetic stirring bars
Spectrophotometer or color comparator
Turbidimeter
pH meter
Assorted measurement pipettes (1, 5, 10 ml) and volumetric pipettes to 50 ml
Burette
Glass or plastic funnels
Ringstands and rings
MATERIALS
Aluminum sulfate solution, 1 g/l or ferric sulfate solution, 1 g/lH2SO4, 2 liters each, 5 x 10-2 M, 10-2 M
NaOH,, 1 liter, 10-1 M
Sodium carbonate, 1 liter each, 5 x 10-2 M, 10-2 M
Indicators: methyl orange, phenolphthalein
Synthetic water sample: Add suspended matter with a kaolin, montmorillonite, illite, or bentonite clay and/or the color with extract from boiled leaves or with instant coffee to raw water. Turbidity might be increased to about 40 turbidity units and color to about 80 color units (Clay suspension sample should be mixed for 3 days).
Buffer solution
Whatman #1 filter paper
REPORT
Prepare tables which facilitate comparisons of coagulant dosages with alkalinity, pH, color, turbidity, and other changes observed. Plot the inverse of turbidity and color versus coagulant dosage as part of the analysis. Plot turbidity versus coagulant dose at different settling times to determine the influence of floc formation and settling characteristics on the selection of coagulant dosage.Comment on the differences between coagulation with iron and aluminum salts. Define the pH ranges over which each salt should result in effective coagulation.
Determine the rate of aggregation for a particular coagulant dose and pH by plotting the reciprocal of the turbidity versus time. (This would represent a second order reaction with respect to turbidity). Also plot the natural log of the reciprocal turbidity (representing a first order reaction) versus time. Determine which gives the best straight line fit of the data and determine the slope. HAND BOOK : ( From ENVO's Practical Experience of Last Ten Years )
Chemical |
PH value
Dose
Aluminium Sulphate(ALUM)
6.5-8.5
70-85 mg/ liter
Ferric Sulphate
8-8.5
35 mg/liter
Ferric Chloride (Used in STP/ETP)
5.5
28-35 mg/liter
Ferrous Sulphate(Used in ETP)
8-8.5
35-70 mg/liter
Saleem Asraf Syed Imdaadullah
Mobile : 9899300371
311/22,Zakir Nagar,New Delhi-110025
email: saleemasraf@gmail.com
BLOG: http://saleemindia.blogspot.com
Mobile : 9899300371
311/22,Zakir Nagar,New Delhi-110025
email: saleemasraf@gmail.com
BLOG: http://saleemindia.blogspot.com
New Delhi, India
New Delhi, Delhi 110001, India
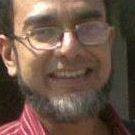
Saturday, July 19, 2008
UPGRADATION OF THE EXISTING SEWAGE TREATMENT PLANT (STP)
UPGRADATION OF THE EXISTING SYSTEM
POINT ONE
: FMR technology in place of existing conventional Activated Sludge System
Utilizing FMR technology can dramatically increase the efficiency of the Aeration system. Compared to conventional technologies the FMR is compact, energy efficient and user friendly. It also allows flexibility in design of the reactor tank.
The FMR is better than SAFF technology and works on the same principle as the submerged fixed film process (SAFF) with only one exception - the media is not fixed and floats around in the aeration tank. The main advantage of this system over the submerged fixed film process is that it prevents choking of the media.
FMR is an advanced version of the SAFF, which uses a floating media to avoid the practical choking problem of media in SAFF.
POINT TWO
:
The existing Sludge drying beds can be replaced with sludge thickener and centrifuge which is faster and efficient for disposal of sludge. It is also hygienic in view of five star hotel.
Sludge Thickening
:
Gravity thickening is accomplished in circular sedimentation basins similar to those used for primary and secondary clarification of liquid wastes
The sludge thickener shall be used to store and gravity thickens sludges from the waste treatment processes. Settled sludges are discharged on an as needed via sludge pumps. Water content in sludge can be reduced by mechanically compressing sludge in filter press, belt press etc. this can also be achieved by centrifuge mechanism and also by other mechanical devices. Excess supernatant wills gravity flow from the tank with provisions for manual decanting of waters via valves located on the side of the tank.
The Area Requirement of Sludge Thickener and Centrifuge:
Both the above items can be installed in the area presently occupied by sludge drying beds. No extra area is required.
POINT THREE
: The media in ACF and PSF are to be changed as they have losed filtration capacity. They have not been changed for a long time. POINT FOUR : The treated water after ACF can be passed through a Softener so that this water can be used in Cooling tower therby reducing consumption of ground water.
Saleem Asraf Syed Imdaadullah
Envo Projects
Mobiles : 9899300371
311/22,Zakir Nagar,New Delhi-110025
email: saleemasraf@gmail.com
web: http://saleemindia.blogspot.com
Envo Projects
Mobiles : 9899300371
311/22,Zakir Nagar,New Delhi-110025
email: saleemasraf@gmail.com
web: http://saleemindia.blogspot.com
New Delhi, India
New Delhi, Delhi 110001, India
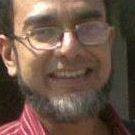
Thursday, October 05, 2006
DATA REQUIRED TO DESIGN ANY ETP/STP/WTP
1. Type Of Waste : Is it dyeing and printing or only dyeing or only printing
2.Total quantity of waste : Not mentioned
3.Total processing hour in a day of 24 hours: Not Mentioned
4. Flow Rate: 40 cu mtr/ Hr
5.Inlet Parameters: pH:-------, TSS:--------, BOD:---------, COD:---------, OIl & Grease:-------, Detergents:-------
6.Outlet parameters required:
7.Available area for the proposed ETP:
8. Do you mean to reuse the treated water or some part of it, if yes how much water and where
New Delhi, India
New Delhi, Delhi 110001, India
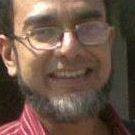
Sunday, August 13, 2006
UASB DESIGN PARAMETERS
UASB Design
In general, there are two ways to design an UASB reactor
If input COD: 5,000 - 15,000 mg/l or more, the design method should be used based on Organic Loading rate, (OLR) If input COD < 5000 mg/l, the design method should be calculated based on velocity.
Some H2S gas can pass the GSL separator and accumulate above the water level in the top of the reactor. This will be oxidized to sulphate by oxygen in the air to form Sulphuric Acid that will in turn cause corrosion of both concrete and steel. Below the water level: Calcium Oxide, (CaO), in concrete can be dissolve with by Carbon Dioxide, (CO2), in the liquid in low pH conditions. To avoid these problems, the material used to construct the UASB reactor should be corrosion resistant, such as stainless steel or plastics, or be provided with proper surface coatings, (e.g. coated concrete rather than coated steel, plastic covered with impregnated hardwood for the settler, plastic fortified plywood, etc).
Operation
Operation criteria: The optimum pH range is from 6.6 to 7.6 The wastewater temperatures should not be < p =" 350"> 20oC) and sometimes the start-up can take up to 3 – 4 months. In start-up process, hydraulic loading must be Ј 50% of the design hydraulic loading.
The start-up of the UASB reactor can be considered to be complete once a satisfactory performance of the system has been reached at its design load.
In general, there are two ways to design an UASB reactor
If input COD: 5,000 - 15,000 mg/l or more, the design method should be used based on Organic Loading rate, (OLR) If input COD < 5000 mg/l, the design method should be calculated based on velocity.
Some H2S gas can pass the GSL separator and accumulate above the water level in the top of the reactor. This will be oxidized to sulphate by oxygen in the air to form Sulphuric Acid that will in turn cause corrosion of both concrete and steel. Below the water level: Calcium Oxide, (CaO), in concrete can be dissolve with by Carbon Dioxide, (CO2), in the liquid in low pH conditions. To avoid these problems, the material used to construct the UASB reactor should be corrosion resistant, such as stainless steel or plastics, or be provided with proper surface coatings, (e.g. coated concrete rather than coated steel, plastic covered with impregnated hardwood for the settler, plastic fortified plywood, etc).
Operation
Operation criteria: The optimum pH range is from 6.6 to 7.6 The wastewater temperatures should not be < p =" 350"> 20oC) and sometimes the start-up can take up to 3 – 4 months. In start-up process, hydraulic loading must be Ј 50% of the design hydraulic loading.
The start-up of the UASB reactor can be considered to be complete once a satisfactory performance of the system has been reached at its design load.
VIDEO
New Delhi, India
New Delhi, Delhi 110001, India
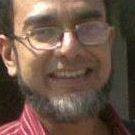
Sunday, July 03, 2005
ETP CHECK LIST
CHECK LIST –ETP ( INDUSTRIAL WASTE/DOMESTIC )
Introduction : Waste water is a combination of liquid and solid waste from residences,industries, commercial buildings, Instituions, together with any surface water which may be present.
Purpose of treatment : To reduce public health hazard of waste water by preventing pathogenic organisms and hazardous waste materials from entering water bodies from which potable water supply is taken out and to minimise the harmful impact of the waste water on the receiving stream and environment.
Sr No Description of item Observations
1 Type of waste ---
a) Domestic----- Municipal sewage water
b) Industrial--- Dyeing,paper,automobile,fertilizer,food processing, electroplating, and others
2 Manufacturing process sheet of concerned industry showing different sources of waste water release and qty
3 Waste water test report
BOD,
TSS,
PH,
TDS,
COD,
Oil & Grease
Detergents
Toxic elements (Chrome, cyanide,nickel etc)
Coliform bacteria
3 Quantity of waste water generated per day
4 Working hours per day
5 Flow rate= Qty/ working hours = liter per hour
6 Location plan of industry showing possible location of ETP/STP
7 If any ETP/STP already exists ? Yes/No
8 Project report of the existing ETP/STP
9 Problems encountered in the existing ETP/STP
10 Waste Water test report of existing ETP/STP at inlet and outlet point
11 Actual sizes of the different units of the existing ETP/STP
12 Whether reuse of treated waste water required ? Yes/No
13 Paper work like Consent application etc Done/ Not Done
14 If not done , whether to apply for
a) Consent to establish
b) NOC
15 Any other information
Contact person : Mr. Phone Number : Office = Res:
Address of Contact person :
Date of our visit :
Introduction : Waste water is a combination of liquid and solid waste from residences,industries, commercial buildings, Instituions, together with any surface water which may be present.
Purpose of treatment : To reduce public health hazard of waste water by preventing pathogenic organisms and hazardous waste materials from entering water bodies from which potable water supply is taken out and to minimise the harmful impact of the waste water on the receiving stream and environment.
Sr No Description of item Observations
1 Type of waste ---
a) Domestic----- Municipal sewage water
b) Industrial--- Dyeing,paper,automobile,fertilizer,food processing, electroplating, and others
2 Manufacturing process sheet of concerned industry showing different sources of waste water release and qty
3 Waste water test report
BOD,
TSS,
PH,
TDS,
COD,
Oil & Grease
Detergents
Toxic elements (Chrome, cyanide,nickel etc)
Coliform bacteria
3 Quantity of waste water generated per day
4 Working hours per day
5 Flow rate= Qty/ working hours = liter per hour
6 Location plan of industry showing possible location of ETP/STP
7 If any ETP/STP already exists ? Yes/No
8 Project report of the existing ETP/STP
9 Problems encountered in the existing ETP/STP
10 Waste Water test report of existing ETP/STP at inlet and outlet point
11 Actual sizes of the different units of the existing ETP/STP
12 Whether reuse of treated waste water required ? Yes/No
13 Paper work like Consent application etc Done/ Not Done
14 If not done , whether to apply for
a) Consent to establish
b) NOC
15 Any other information
Contact person : Mr. Phone Number : Office = Res:
Address of Contact person :
Date of our visit :
Labels:
CHECK LIST,
etp,
STP
New Delhi, India
New Delhi, Delhi 110001, India
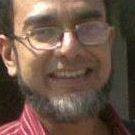
Saturday, August 28, 2004
Eastern Envo Protect Guwahati Assam India, my baby
My own Brand is "ENVO". My company ENVO PROJECTS is based is New Delhi and in the service of the nation since 1994.
Eastern Envo Protect ,Guwahati, Assam , India is One another company i helped to create and the founder syed mehdi hussain absorbed my staff bubu , abul etc from my Delhi based company Envo Projects, New Delhi. www.envo.8m.com.One another wonderful experience of life.Our first project in assam is Pragati Hospital & Research Center,NH Bypass,Sivsagar,Assam where we installed Incinerator for bio medical waste management for which i brought old Ali Miya from Delhi to make the plant.Ali Miya is former employee of M/s Thermax Ltd.
**"""""""*********"""""""""********"""""
Eastern Envo Protect ,Guwahati, Assam , India is One another company i helped to create and the founder syed mehdi hussain absorbed my staff bubu , abul etc from my Delhi based company Envo Projects, New Delhi. www.envo.8m.com.One another wonderful experience of life.Our first project in assam is Pragati Hospital & Research Center,NH Bypass,Sivsagar,Assam where we installed Incinerator for bio medical waste management for which i brought old Ali Miya from Delhi to make the plant.Ali Miya is former employee of M/s Thermax Ltd.
**"""""""*********"""""""""********"""""
Sir,
We have degraded the gift called NATURE given to us by Almighty GOD to a level from where recovery is next to impossible because of heavy expenditure involved. Take the case of Bharalu river .Can you now call it a river????? And what can you do about it now?????? Any ideas . The only thing you can do now is public awerness. The people who are staying on the banks of the bharalu river and have well or tube well or borewell as their drinking water source are consuming bacteria(E-COLI) alongwith the water. The ground water has become polluted. You can initiate a study , test the ground water along the river banks and publish the results in main daily news papers. associate PHE Deptt or IIT,guwahati ,otherwise people will not believe you.You can generate funds for the study from WHO.
Same is the case with Tuklai of Jorhat.
Thanx for your letter and your new mail id.
---saleem
----- Original Message -----
From: Eastern envoSent: Friday, August 27, 2004 9:53 AM
Due to an increase in unplanned urbanization and industrialization, the environment has deteriorated significantly. Pollution from a wide variety of emissions, such as from automobiles and industrial activities, has reached critical levels in many urban and industrial areas, causing respiratory, ocular and other health problems. Monitoring of the urban environment in selected cities in recent years by the pollution control authority has identified 21 critically polluted areas in the country.
Agricultural activities including widespread use of fertilizers, pesticides and weed killers also alter the environment and create health hazards. Water stagnation and the consequent multiplication of vectors has increased the risk of vector-borne diseases. The risk associated with disposal of hospital wastes has added to the overall unhealthy situation.
India is a party to the UN Conference on Environment and Development (UNCED) held in 1992. In the same year, a national conservation strategy and a policy statement on environment were formulated. The policy addresses issues related to sustainable development including health. Thrust has also been given to management of hazardous waste, adoption of clean technologies by industries, establishment of effluent treatment plants, criteria for environmentally friendly products, phasing out of ozone depleting substances, and creating mass awareness programmes.
A very far-reaching notification by the Ministry of Environment and Forests gazetted in 1994 makes it obligatory for almost all development projects to conduct an environmental impact assessment study which has to be evaluated by an impact assessment agency. A Government constituted group at the highest level has identified six priority programme areas, namely urban low cost sanitation, urban waste water management, urban solid waste management including hospital waste management, rural environmental sanitation, industrial waste management and air pollution control, and strengthening of health surveillance and support services. These areas have been addressed in the Dayal Committee Report that forms the basis for a comprehensive national programme on sanitation and environmental hygiene.
There are many constitutional provisions and laws pertaining to the environment and its protection and improvement. However, the level of enforcement has been extremely poor. Besides, there is no comprehensive legislation on environment and health. In view of the current situation and the Dayal Committee Report, it was proposed that action be taken by the concerned ministries/departments to prioritize the areas and activities that should be included in the 9th plan. During the 9th FYP the Ministry has proposed the following actions:
Strengthen environmental health and health risk assessment in the country. A division of environmental health will be established in the Department of Health for this purpose.
Establish a hospital waste management programme.
Initiate drinking water quality surveillance as a part of disease surveillance.
mehdi 27.8.2000
MY STAFF MEMBER SYED BUBU HASAN AT OUR STP PROJECT SITE HOTEL OBEROI MAIDENS,DELHI
Labels:
envo,
envo projects,
etp,
STP
New Delhi, India
New Delhi, Delhi, India
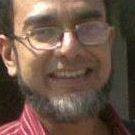
Subscribe to:
Posts (Atom)