Bleaching powder dosing for disinfection in waste water treatment plant
Sources of Informations given below
Manual http://cpheeo.gov.in/upload/uploadfiles/files/Chapter%206-9.pdf
1. https://www.epa.ie/pubs/advice/drinkingwater/Disinfection2_web.pdf
2.http://jeb.co.in/journal_issues/200710_oct07/paper_04.pdf
The pilot scale disinfection units located at two
different UASBR based STPs have been selected for this study.
One of these pilot plants has been constructed after 27 MLD UASBR
based STP, Noida (Uttar Pradesh, India) and is based on
chlorination using calcium hypochlorite (either slurry form or liquid
high test hypochlorite, HTH) with a capacity of 2 million liter per day
(MLD). The other 1 MLD DHS-biotower pilot plant, developed by
Prof. H. Harada (Machdar et al., 1997), is based on fixed film
aerobic process and has been constructed after 40 MLD UASBR
based STP, Karnal (Haryana, India). These STPs, based on
UASBR technology, consists of preliminary treatment (Screen and
Grit Chamber), UASBR and final polishing pond (Fig. 1).
A schematic diagram of the pilot plants at Noida and Karnal
is presented in Fig. 2 and 3 respectively. The chlorination unit of 2
MLD consists of a sump, mixing unit and baffled contact chamber
(3m x 7m) and a specific dose of chlorine was mixed with a separate
pipe. The 1 MLD DHS-biotower based on fixed film aerobic process
consists of a sump and reactor having plastic rectangular sheets
onto which triangular prism polyurethane foams were tiled. Raw
sewage after UASBR treatment was supplied to the chlorination unit
and DHS-biotower
In case of chlorination unit, initially the bleaching powder
was used as a disinfectant from day 1 to day 48 and later on it was
found that there was no residual chlorine in the bleaching powder,
so the bleaching powder was replaced with calcium hypochlorite as
disinfectant after 48th day. The dose of disinfectant was 5 mgl-1 from
day 1 to day 16 and was increased to 20 mgl-1 from day 20. The
contact time for the reaction between wastewater and disinfectant
was 30 min throughout the study.
Results and Discussion
Reduction of fecal coliform: To achieve good disinfection, the
contact time and dose are extremely important. A longer contact time
is required for complete disinfection to occur. As per Lindsay (2004),
a contact time of 30 minutes is a minimum, and if the dose remains
constant, the contact time may necessitated to be increased at low
temperatures or higher pH to obtain the same level of disinfection.
Typical chlorine doses for municipal wastewater disinfection are
about 5-20 mgl-1 with a contact time of 30 to 60 min (Lazarova et al.,
1999). During this study, 5 and 20 mgl-1 of disinfectant doses for a
fixed contact time of 30 min was applied. It was observed that a dose
of 20 mgl-1 was very effective for the reduction in indicator
microorganism (fecal coliforms). Initially when a dose of 5 mgl-1 was
used, the reduction in fecal coliforms count was less than 90%. It
may be attributed to the fact that the minimum dose required for the
killing of microorganism was not sufficient as there was high chlorine
demand due to the presence of high concentration of organic matter
and suspended solids in the UASBR effluent. The average fecal
coliforms count was reduced from 3.58 x 105
(± 1.02 x 105
) MPN/
100ml to nil at a dose of 20 mgl-1 and 30 min contact time (Fig. 4a).
Thus the results shows that almost 100% removal of fecal coliforms
has been observed after chlorination; however at certain days i.e.,
from day 7 to day 14 and from day 44 to day 53 (Fig. 4a), the
number of fecal coliforms present in the wastewater effluent after
disinfection was increased. It could be explained on the basis of
type of chemical used for the chlorination. During this period,
bleaching powder was used. Later on it was found that the chemical
used at the plant does not have any residual chlorine. Chlorination
was switched to the fortified brand of the calcium hypochlorite, high
test hypochlorite (HTH). It indicated that chlorination was very effective
in the removal of fecal coliforms if the regular operation and
maintenance (O and M) is ensured.
COPY RIGHTS : TO AVOID COPYRIGHT VIOLATIONS, ALL POSTS ARE SHOWN ALONG WITH SOURCES FROM WHERE ITS TAKEN. PLEASE CONTACT ME IN MY EMAIL SALEEMASRAF@GMAIL.COM , IF YOU ARE THE AUTHOR AND YOUR NAME IS NOT DISPLAYED IN THE ARTICLE.THE UNINTENTIONAL LAPSE ON MY PART WILL BE IMMEDIATELY CORRECTED.
I HAVE SHARED ALL MY PRACTICAL WATER TREATMENT EXPERIENCES WITH SOLVED EXAMPLE HERE SO THAT ANYBODY CAN USE IT.
SEARCH THIS BLOG BELOW FOR ENVO ,COMPACT STP,ETP,STP,FMR,MBBR,SAFF,IRON,ARSENIC,FLUORIDE,FILTER,RO,UASB,BIO GAS,AERATION TANK,SETTLING TANK,DOSING,AMC.
SEARCH THIS BLOG
Showing posts with label dosing. Show all posts
Showing posts with label dosing. Show all posts
Thursday, December 05, 2019
Bleaching powder dosing for disinfection in waste water treatment plant
Labels:
bleaching powder,
disinfection,
dosing,
etp,
STP,
wtp
New Delhi, India
New Delhi, Delhi, India
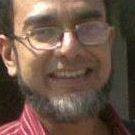
Sunday, September 14, 2008
determinatin of optimum alum dose
INTRODUCTION The main difficulty is to determine the optimum coagulant dosage related
to the influent of raw water. Excessive coagulant overdosing leads to increased treatment costs and public health concerns, while underdosing leads to a failure to meet the water quality targets and less efficient
operation of the water treatment plant.
Manual methods mainly include jar testing
Jar testing involves taking a raw water sample and applying different quantities of coagulant to each sample. After a short period of time each sample is assessed for water quality and the dosage that produces the optimal result is used as a set point.
Operators change the dose and make a new jar test if the quality of treated water changes.
OBJECTIVES
To conduct jar test on a natural surface water in order to estimate an optimum dosage of aluminum sulfate or ferric sulfate for the removal of suspended matter , To observe the rate of floc formation and sedimentation.
The dose of coagulant which gives the best floc is the optimum dose of coagulants.
PROCEDURE
A. DETERMINE OF OPTIMUM COAGULANT DOSAGE- Collect 20 to 50 liters of a natural surface water. Analyze the water for pH, turbidity, color after filtration, and alkalinity.
- Alternatively, make up a synthetic water sample for testing. Record both the water temperature and ambient air temperature.
- Calculate the amount of alkalinity required to react with the maximum dosage of aluminum or ferric sulfate. If necessary, augment the natural alkalinity by the addition of 0.1 N Na2CO3 so that the alkalinity will be at least 0.5 meq/l (25 mg/l as CaCO3).
- Measure exact 1 liter of water into each jar test reactor. Prepare portions of the aluminum or ferric sulfate solution which will yield 10 to 50 mg/l as Al2O3 or Fe2O3 when added to the sample aliquots.
- Mix at 50 rpm to ensure water is completely mixed.
- Measure chemical volumes to achieve desired dose in each reactor.
- Increase mixing speed to 250 rpm. Add the chemicals to each reactor near the vortex. All reactor should be dosed at the same time.
- Rapid mix for 1 min.
- Reduce mixing to 60 rpm for 9 min.; Observe the reactors at 3 min. intervals to detect the formation of flocs. Reduce mixing to 25 rpm for 4 min.; Reduce mixing to 10 rpm for 2 min.
- Turn off mixers and allow particles to settle for 20 min.
Measure the turbidity or color, alkalinity, and pH of the liquid in each jar by sampling at the top, taking care not to disturb the sediment in sampling. Measure the depth of sludge in the beaker.
Measure final pH, turbidity or color of the supernatant of each sample. Measure the depth of sludge in the beaker.
Plot turbidity or color versus pH.
EFFECT OF MIXING (AGGREGATION KINETICS)
Prepare identical (optimum) coagulant dosages for all six beakers.Use the same rapid mix as before but vary the time of slow mix at 30 rpm. Use 5, 10, 15, 20, 30, and 45 minutes for the six jars respectively. Terminate mixing by carefully lifting the paddle from the beaker at appropriate time.
Allow 30 minutes for settling.
Measure the color or turbidity and pH of the supernatant in each beaker.
APPARATUS
Jar test apparatus and beakersMagnetic stirrer plus magnetic stirring bars
Spectrophotometer or color comparator
Turbidimeter
pH meter
Assorted measurement pipettes (1, 5, 10 ml) and volumetric pipettes to 50 ml
Burette
Glass or plastic funnels
Ringstands and rings
MATERIALS
Aluminum sulfate solution, 1 g/l or ferric sulfate solution, 1 g/lH2SO4, 2 liters each, 5 x 10-2 M, 10-2 M
NaOH,, 1 liter, 10-1 M
Sodium carbonate, 1 liter each, 5 x 10-2 M, 10-2 M
Indicators: methyl orange, phenolphthalein
Synthetic water sample: Add suspended matter with a kaolin, montmorillonite, illite, or bentonite clay and/or the color with extract from boiled leaves or with instant coffee to raw water. Turbidity might be increased to about 40 turbidity units and color to about 80 color units (Clay suspension sample should be mixed for 3 days).
Buffer solution
Whatman #1 filter paper
REPORT
Prepare tables which facilitate comparisons of coagulant dosages with alkalinity, pH, color, turbidity, and other changes observed. Plot the inverse of turbidity and color versus coagulant dosage as part of the analysis. Plot turbidity versus coagulant dose at different settling times to determine the influence of floc formation and settling characteristics on the selection of coagulant dosage.Comment on the differences between coagulation with iron and aluminum salts. Define the pH ranges over which each salt should result in effective coagulation.
Determine the rate of aggregation for a particular coagulant dose and pH by plotting the reciprocal of the turbidity versus time. (This would represent a second order reaction with respect to turbidity). Also plot the natural log of the reciprocal turbidity (representing a first order reaction) versus time. Determine which gives the best straight line fit of the data and determine the slope. HAND BOOK : ( From ENVO's Practical Experience of Last Ten Years )
Chemical |
PH value
Dose
Aluminium Sulphate(ALUM)
6.5-8.5
70-85 mg/ liter
Ferric Sulphate
8-8.5
35 mg/liter
Ferric Chloride (Used in STP/ETP)
5.5
28-35 mg/liter
Ferrous Sulphate(Used in ETP)
8-8.5
35-70 mg/liter
Saleem Asraf Syed Imdaadullah
Mobile : 9899300371
311/22,Zakir Nagar,New Delhi-110025
email: saleemasraf@gmail.com
BLOG: http://saleemindia.blogspot.com
Mobile : 9899300371
311/22,Zakir Nagar,New Delhi-110025
email: saleemasraf@gmail.com
BLOG: http://saleemindia.blogspot.com
New Delhi, India
New Delhi, Delhi 110001, India
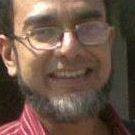
Subscribe to:
Posts (Atom)