please look at:
COPY RIGHTS : TO AVOID COPYRIGHT VIOLATIONS, ALL POSTS ARE SHOWN ALONG WITH SOURCES FROM WHERE ITS TAKEN. PLEASE CONTACT ME IN MY EMAIL SALEEMASRAF@GMAIL.COM , IF YOU ARE THE AUTHOR AND YOUR NAME IS NOT DISPLAYED IN THE ARTICLE.THE UNINTENTIONAL LAPSE ON MY PART WILL BE IMMEDIATELY CORRECTED.
I HAVE SHARED ALL MY PRACTICAL WATER TREATMENT EXPERIENCES WITH SOLVED EXAMPLE HERE SO THAT ANYBODY CAN USE IT.
SEARCH THIS BLOG BELOW FOR ENVO ,COMPACT STP,ETP,STP,FMR,MBBR,SAFF,IRON,ARSENIC,FLUORIDE,FILTER,RO,UASB,BIO GAS,AERATION TANK,SETTLING TANK,DOSING,AMC.
SEARCH THIS BLOG
Sunday, September 14, 2008
homeopthaic remedy for bed wetting in children http://abchomeopathy.com/c.php/173
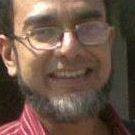
determinatin of optimum alum dose
INTRODUCTION The main difficulty is to determine the optimum coagulant dosage related
to the influent of raw water. Excessive coagulant overdosing leads to increased treatment costs and public health concerns, while underdosing leads to a failure to meet the water quality targets and less efficient
operation of the water treatment plant.
Manual methods mainly include jar testing
Jar testing involves taking a raw water sample and applying different quantities of coagulant to each sample. After a short period of time each sample is assessed for water quality and the dosage that produces the optimal result is used as a set point.
Operators change the dose and make a new jar test if the quality of treated water changes.
OBJECTIVES
To conduct jar test on a natural surface water in order to estimate an optimum dosage of aluminum sulfate or ferric sulfate for the removal of suspended matter , To observe the rate of floc formation and sedimentation.
The dose of coagulant which gives the best floc is the optimum dose of coagulants.
PROCEDURE
A. DETERMINE OF OPTIMUM COAGULANT DOSAGE- Collect 20 to 50 liters of a natural surface water. Analyze the water for pH, turbidity, color after filtration, and alkalinity.
- Alternatively, make up a synthetic water sample for testing. Record both the water temperature and ambient air temperature.
- Calculate the amount of alkalinity required to react with the maximum dosage of aluminum or ferric sulfate. If necessary, augment the natural alkalinity by the addition of 0.1 N Na2CO3 so that the alkalinity will be at least 0.5 meq/l (25 mg/l as CaCO3).
- Measure exact 1 liter of water into each jar test reactor. Prepare portions of the aluminum or ferric sulfate solution which will yield 10 to 50 mg/l as Al2O3 or Fe2O3 when added to the sample aliquots.
- Mix at 50 rpm to ensure water is completely mixed.
- Measure chemical volumes to achieve desired dose in each reactor.
- Increase mixing speed to 250 rpm. Add the chemicals to each reactor near the vortex. All reactor should be dosed at the same time.
- Rapid mix for 1 min.
- Reduce mixing to 60 rpm for 9 min.; Observe the reactors at 3 min. intervals to detect the formation of flocs. Reduce mixing to 25 rpm for 4 min.; Reduce mixing to 10 rpm for 2 min.
- Turn off mixers and allow particles to settle for 20 min.
Measure the turbidity or color, alkalinity, and pH of the liquid in each jar by sampling at the top, taking care not to disturb the sediment in sampling. Measure the depth of sludge in the beaker.
Measure final pH, turbidity or color of the supernatant of each sample. Measure the depth of sludge in the beaker.
Plot turbidity or color versus pH.
EFFECT OF MIXING (AGGREGATION KINETICS)
Prepare identical (optimum) coagulant dosages for all six beakers.Use the same rapid mix as before but vary the time of slow mix at 30 rpm. Use 5, 10, 15, 20, 30, and 45 minutes for the six jars respectively. Terminate mixing by carefully lifting the paddle from the beaker at appropriate time.
Allow 30 minutes for settling.
Measure the color or turbidity and pH of the supernatant in each beaker.
APPARATUS
Jar test apparatus and beakersMagnetic stirrer plus magnetic stirring bars
Spectrophotometer or color comparator
Turbidimeter
pH meter
Assorted measurement pipettes (1, 5, 10 ml) and volumetric pipettes to 50 ml
Burette
Glass or plastic funnels
Ringstands and rings
MATERIALS
Aluminum sulfate solution, 1 g/l or ferric sulfate solution, 1 g/lH2SO4, 2 liters each, 5 x 10-2 M, 10-2 M
NaOH,, 1 liter, 10-1 M
Sodium carbonate, 1 liter each, 5 x 10-2 M, 10-2 M
Indicators: methyl orange, phenolphthalein
Synthetic water sample: Add suspended matter with a kaolin, montmorillonite, illite, or bentonite clay and/or the color with extract from boiled leaves or with instant coffee to raw water. Turbidity might be increased to about 40 turbidity units and color to about 80 color units (Clay suspension sample should be mixed for 3 days).
Buffer solution
Whatman #1 filter paper
REPORT
Prepare tables which facilitate comparisons of coagulant dosages with alkalinity, pH, color, turbidity, and other changes observed. Plot the inverse of turbidity and color versus coagulant dosage as part of the analysis. Plot turbidity versus coagulant dose at different settling times to determine the influence of floc formation and settling characteristics on the selection of coagulant dosage.Comment on the differences between coagulation with iron and aluminum salts. Define the pH ranges over which each salt should result in effective coagulation.
Determine the rate of aggregation for a particular coagulant dose and pH by plotting the reciprocal of the turbidity versus time. (This would represent a second order reaction with respect to turbidity). Also plot the natural log of the reciprocal turbidity (representing a first order reaction) versus time. Determine which gives the best straight line fit of the data and determine the slope. HAND BOOK : ( From ENVO's Practical Experience of Last Ten Years )
Chemical |
PH value
Dose
Aluminium Sulphate(ALUM)
6.5-8.5
70-85 mg/ liter
Ferric Sulphate
8-8.5
35 mg/liter
Ferric Chloride (Used in STP/ETP)
5.5
28-35 mg/liter
Ferrous Sulphate(Used in ETP)
8-8.5
35-70 mg/liter
Saleem Asraf Syed Imdaadullah
Mobile : 9899300371
311/22,Zakir Nagar,New Delhi-110025
email: saleemasraf@gmail.com
BLOG: http://saleemindia.blogspot.com
Mobile : 9899300371
311/22,Zakir Nagar,New Delhi-110025
email: saleemasraf@gmail.com
BLOG: http://saleemindia.blogspot.com
New Delhi, India
New Delhi, Delhi 110001, India
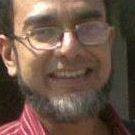
ITS A BIO GAS PLANT FROM SOLID WASTE
----- Original Message -----
To: goswami vivekSent: Sunday, September 14, 2008 2:42 PMSubject: ITS A GAS BIO GAS
San Antonio in the United States could become the first city to draw all its energy requirements from methane gas generated from the city's water treatment system through recycling 14,000 tonnes of biosolids in sewage annually. The methane source includes human waste that, if left untreated and unutilised, would only pollute soil and water.
Treating bio-waste, however, could generate an average of 1.5 million cubic feet of gas a day - enough to fill 1,250 tanker trucks daily - according to the system's chief operating officer. A by-product of human and organic waste, methane is the chief component of natural gas that can fuel generators, power plants and furnaces.
Closer home, gobar gas - natural gas obtained from methane released by cattle waste - as a green alternative to diesel and other fossil fuels has been taken up seriously, particularly in rural households. However, a lack of adequate hygiene is a constraint because the gas formation - in the large containers filled with gobar - makes the drum's lid rise, and there is spillage all around the plant. So, in India gobar gas plants are fertile breeding grounds for mosquitoes and other pests. But this is not an insurmountable problem. Gobar gas plants could be expanded and diversified to include energy extraction from all kinds of biomass and the gas so produced could fuel power stations - as San Antonio proposes to do - and with improved sanitation, the experiment could yield good results for several Indian cities.
As a renewable resource, biomass - either from plants, agriculture and forestry residues, animal or human waste - is biodegradable and so is far more eco-friendly than petroleum-derived fuels. And they are relatively easier to source and process, unlike the sophisticated instruments and know-how required to extract oil or refine coal. Ethanol derived from biofuels has a very high octane rating. It might deliver less energy than gasoline, but by blending about 10 per cent ethanol and petrol or diesel together, a feasible balance is achieved with no perceptible effect on fuel economy.
America's space agency NASA is sponsoring a joint project to turn human waste into a power source for spaceships using a process that could also produce other chemicals that can be used on board. Instead of turning up our noses at the idea of recycling human waste and other biosolids in sewage, it would be worthwhile to explore fully and exploit the immense potential hidden in what we routinely regard as being useless.
New Delhi, India
New Delhi, Delhi, India
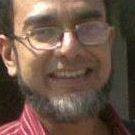
Subscribe to:
Posts (Atom)