Waste disposal is one of the major problems being faced by all nations across the globe. The daily per capita solid waste generated in India ranges from about 100 g in small towns to 500 g in large towns. It takes anywhere between three and seven days for the waste to be disposed from the time of its generation. Major portion of the collected waste is dumped in landfill sites. The recyclable content of waste ranges from about 13% to 20%. In a developing country like India, paper, plastic, glass, rubber, ferrous and non-ferrous metals all the material that can be recycled are salvaged from this waste to produce low-cost products extensively used by the lower-income groups of the society. However, data collected from 44 Indian cities have revealed that about 70% of them do not have adequate capacity for collection and transportation of MSW (municipal solid waste) (Pachauri and Sridharan 1998). The uncollected waste that usually finds its way in sewers is eaten by the cattle, or left to rot in the open, or burnt on roadsides.
In the face of burgeoning urban populations and growing mounds of garbage, initiatives like converting garbage into energy could show the way for cities. A private company has begun converting the city's garbage into fuel pellets and now plans to establish a 10 MW power plant. According to TIFAC (Technology Information Forecasting and Assessment Council), Delhi, Mumbai, and Calcutta would be generating 5000 tonnes of garbage every day, in about a decade, and disposal would be difficult. The existing dumping years would create enormous pollution and health hazards. Municipal authorities would find it expensive to transport garbage and dispose it of scientifically, according to a TIFAC data sheet on 'Fuel pellets from municipal waste'. As part of a pilot project for integrated waste management, the Department of Science and Technology had established a prototype fuel pelletization plant at Deonar, Mumbai, in the early 1990s. The plant was designed to process Indian garbage. The garbage was first dried to bring down the high moisture levels. Sand, grit, and other incombustible matter were then mechanically separated before the garbage was compacted and converted into pellets. Fuel pellets have several distinct advantages over coal and wood, according to the TIFAC data sheet. It is cleaner, free from incombustibles, has lower ash and moisture contents, is of uniform size, cost-effective, and eco-friendly (The Hindu, 2 May 2000).
Table 1 Estimated quantity of waste generated in India
In addition to MSW, large quantity of waste, in both solid and liquid forms, is generated by the industrial sector like breweries, sugar mills, distilleries, food-processing industries, tanneries, and paper and pulp industries. Out of the total pollution contributed by industrial subsectors, 40% to 45% of the total pollutants can be traced to the processing of industrial chemicals and nearly 40% of the total organic pollution to the food products industry alone. Food products and agro-based industries together contribute 65% to 70% of the total industrial waste water in terms of organic load (Pachauri and Sridharan 1998a). Table 1 gives an estimate of waste generated in India by various sectors and industries.Source Bakthavatsalam (1999)
Waste Quantity Municipal solid waste 27.4 million tonnes/year Municipal liquid waste (121 class I and II cities) 12145 million litres/day Distillery (243 nos) 8057 kilo litres/day Pressmud 9 million tonnes/year Food and fruit processing waste 4.5 million tonnes/year Willow dust 30000 tonnes/year Dairy industry waste (COD level 2 kg/m3) 5060 million litres/day Paper and pulp industry waste (300 mills) 1600 m3 waste water/day Tannery (2000 nos) 52500 m3 waste water/day
In addition, the daily per capita sewage generation is about 150 litres. The total sewage generated in India, about 5 billion litres/day in 1947, grew to 30 billion litres/day in 1997. However, the total treatment capacity available is only about 10% of this quantum generated. It is estimated that under the Ganga Action Plan, 46 000 Nm3 (normal cubic metre) of biogas can be produced daily from the sewage treatment plants in 21 Indian cities by treating about 339 million litres/day of municipal waste water. This, with appropriate biogas power plants, will generate total electrical energy of 99 450 kWh/day (Singh 1996).Table 2 Estimated renewable energy potential in India
The urban municipal waste (both solid and liquid) industrial waste coming from dairies, distilleries, pressmud, tanneries, pulp and paper, and food processing industries, etc., agro waste and biomass in different forms if treated properly, has a tremendous potential for energy generation as shown in Table 2.Source Bakthavatsalam (1999)
Energy source Estimated potential Bio energy 17000 MW Draught animal power 30000 MW Energy from MSW 1000 MW Biogas plants 12 million plants
Last year, the INSWAREB (Institute of Solid Waste Research and Ecological Balance) came up with the theory that rice husk, a cheap by-product of paddy milling, has the potential to galvanize the electricity-starved rural India. With a gross calorific value of 3000 kcal/kg, rice husk, capable of high-efficiency combustion, could serve as the fuel for mini power plants of 1 to 2 MW capacity that can be set up in rural areas. The RHA (rice husk ash), obtained as a by-product by burning it, can generate power in the process.
The cost of establishing and maintaining the mini power plant can be easily made good by exporting RHA, which can fetch $50 a tonne. INSWAREB has drawn an action plan for promoting RHA fully exploiting its export potential. It proposes to initiate a couple of mini power plants to popularize the theme. (The Hindu, 9 February 1999).
Similarly, at an inter-ministerial meeting involving the ministries of power, environment and forests, and urban affairs and employment, it was decided to encourage the use of fly ash bricks in all construction activities. The NTPC (National Thermal Power Corporation) had thought of setting up two fly ash brick manufacturing plants at Badarpur and Dadri near Delhi; the theory being that fly ash, apart from being used as a substitute for bricks, could also be utilized for the embankment of roads.The enormous amount of ash generated in Indian thermal power stations poses a serious threat to the environment. In principle, this problem can be tackled by using fly ash in building construction. Increased awareness and use of fly ash bricks, which is stronger (100 kg/cm2 compared to 5075 kg/cm2 of conventional bricks) and smoother on the sides (reducing plastering costs significantly), can provide an eco-friendly solution. Fly ash bricks are better than traditional bricks in the sense also that ash bricks do not use the top fertile soil of the earth, thus protecting the land from agricultural use. Located at the south-east corner of Delhi, the BTPS (Badarpur Thermal Power Station) meets more than 25% of the energy consumption of the capital. It also produces a staggering amount of ash every day (almost 5000 tonnes). The station has, however, been making concrete efforts in ash utilization as a responsible corporate citizen. It has given a major thrust in ash utilization through the manufacture of bricks from fly ash. At present, it has seven units given to private contractors, which manufacture around 16 000 bricks every day. The BTPS had installed a pilot-cum-demonstration plant at its ash dyke way back in 1993. The station adopted the FAL-G technology for the manufacture of ash bricks, which does not require firing or autoclaving. These bricks require natural drying and hence are totally energy-efficient and environment-friendly (The Financial Express, 4 April 1999).
It was also estimated that an energy-from-waste plant, which was to be set up in Scotland, would annually convert 120 000 tonnes of the city's municipal and commercial waste into electricity. It as also to deal with small amounts of non-hazardous clinical and liquid wastes. Besides generating adequate electricity for the plant's in-house needs of around 2.2 MW, it would sell 8.3 MW to the National Grid, electricity distribution network of UK. The facility incorporated two separate systems fuel processing and combustion.To produce the fuel, incoming waste is fed into one of the two hammer mills, where it is shredded into coarse floc material. Each of the mills handles 30 tonnes of waste an hour, almost double the plant's throughput of 15.6 tonnes an hour. The over-capacity allows for unplanned downtime. Magnets remove ferrous materials before the floc is carried by conveyor to a fuel-storage building capable of holding enough for two days operationabout 800 tonnes of refuse-derived fuel (The Hindu, 21 October 1999).
Scientists have developed a technique to treat foul-smelling polluted distillery wastes, using energy from the sun and a chemical catalyst. Tests on a small laboratory-type reactor showed that the method can detoxify 100 litres of diluted distillery waste water in five days. Results of the project at the NARI (Nimbkar Agriculture Research Institute) at Phaltan in Maharashtra were submitted to the MNES (Ministry of Non-conventional Energy Sources). The scientists had applied for a patent on the chemical catalyst. The emphasis after this was to try to improve the technique so that waste treatment is over in just two days. The NARI scientists had taken cues from work on solar detoxification of ground-water and industrial wastes using titanium dioxide catalyst.
By purifying biogas produced from distillery wastes, scientists claimed to have generated huge quantities of com-pressed methane, a gas with immense potential as an alternative source of vehicle fuel. Experimenting with bulk distillery wastes from alcohol manufacturing breweries, researchers from the chemical engineering department of the Jadavpur University produced the gas by a process called biomethanation of the effluents. The process, which also cuts down on the environment pollution, has proved to be an eco-friendly energy production method (The Observer of Business and Politics 25 April 2000).
TERIscientists has been developing new technologies to tackle the problem of waste management
TERI has developed a high-rate digester for fibrous and semi-solid municipal waste with the promise of revolutionizing the waste disposal industry. Described as TEAM (TERI Enhanced Acidification and Methanation) process, for which the patent has also been filed, the digester is said to be quick, economically viable, and suitable for food and agro-based industries and markets. In the face of evident environmental drawbacks of waste disposal methods like land-filling and incineration, the process of biomethanation of waste by anaerobic digestion has economical and social benefits apart from being environment-friendly (The Hindu, 18 March 2000).
TERI began work on the development of a high-rate digester for fibrous and semi-solid MSW in 1996. TEAM process is the culmination of these efforts. The salient features of TEAM are listed below.
Lowered retention time (7 days) and plant area for the whole process to make it economically viable as compared to conventional single phase reactors (3040 days) or aerobic composting (3 to 6 months)
Complete elimination of engineering problems like scum formation, floating of feed leading to incomplete digestion, feed flow problem, etc.
Technology suitable for adoption by small entrepreneurs
Low water consumption because of reuse of the UASB reactor overflow to acidification reactor
Production of good quality biogas, which can be used for power generation or thermal application like cooking or production of process steam as per the needs,
The decrease in total volume of the feed stock after decomposition is more than 50%
The residue after drying is good organic manure.
Currently, a bench-scale plant for processing 50 kg of vegetable waste per day is operational at the Gual Pahari campus of TERI, at Gurgaon, and efforts are under way for upscaling.
The wastes generated by various sectors need to be assessed and evaluated for their energy potential or reuse in any other form. Biomethanation has emerged as the best option for the treatment of high organic content liquids for energy generation. The use of this technology to Indian MSW is still in its developmental stage. Once a commercially proven technology is established, it will go a long way in dealing with energy problems in the country.
COPY RIGHTS : TO AVOID COPYRIGHT VIOLATIONS, ALL POSTS ARE SHOWN ALONG WITH SOURCES FROM WHERE ITS TAKEN. PLEASE CONTACT ME IN MY EMAIL SALEEMASRAF@GMAIL.COM , IF YOU ARE THE AUTHOR AND YOUR NAME IS NOT DISPLAYED IN THE ARTICLE.THE UNINTENTIONAL LAPSE ON MY PART WILL BE IMMEDIATELY CORRECTED.
I HAVE SHARED ALL MY PRACTICAL WATER TREATMENT EXPERIENCES WITH SOLVED EXAMPLE HERE SO THAT ANYBODY CAN USE IT.
SEARCH THIS BLOG BELOW FOR ENVO ,COMPACT STP,ETP,STP,FMR,MBBR,SAFF,IRON,ARSENIC,FLUORIDE,FILTER,RO,UASB,BIO GAS,AERATION TANK,SETTLING TANK,DOSING,AMC.
SEARCH THIS BLOG
Wednesday, November 30, 2005
Re: energy recovery from dairy waste
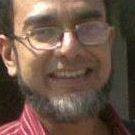
Subscribe to:
Post Comments (Atom)
No comments:
Post a Comment